Lead-Tin Solder
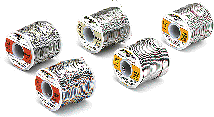
Wire Solder
- Wire solder comes in various diameters from as small as .020" to as large as .0625". It can come as solid core or with rosin inside of it. Rosin gives the solder better flow characteristics onto the objects being soldered together. It usually comes in combinations of 70Sn/30Pb, 60Sn/40Pb, or 63Sn/37Pb. As you probably know from looking at the phase diagram of Pb-Sn, the lowest meltiing point of a Pb-Sn mixture is when they are mixed in a ratio of 63Sn/37Pb. Now you know why solder is made the way it is.
- The Eutectoid Phase diagram of Lead-Tin Solder was very important in the developement of solders. As seen on the Eutectoid phase diagram, the melting point of standard 63Sn/37Pb solder is about 183 degrees C. For most common applications, this temperature is adequate and also easily reached by small, low wattage soldering irons.
- In certain applications involving the flow of high currents through the soldered joint, or the desire to have a solder made of something with less electrical resistance, Ag-Sn solder is used. The Ag in the solder has a much higher electrical conductivity than does the lead. It is however, more expensive and therefore usually reserved for high performance applications. Circuit boards that run equipment on nuclear reactors is one such application.
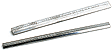
Bar Solder
- The picture above is of bar solder. In most industrial applications today, the wire solder pictured at top is used. Bar solder finds use in large scale applications of industry wherre lots of solder is used on a regular basis. Another use is in the making of stained glass windows. Due to the large quantity of solder needed for making a stained glass window, and the desire to not have any rosin in the core of the solder, bar solder is used.
Andrew Johnson 4/28/96
http://www.eng.vt.edu/eng/materials/classes/MSE2094_NoteBook/
96ClassProj/examples/leadtin.html
Project Hompage | Examples Page